「世界のものづくりを変えた」といわれるトヨタの生産方式を解りやすくまとめました。実は、どの業界にも通じるノウハウが詰まっています。 [/voice][aside]この記事でわかること
・トヨタ生産方式の考え方
・トヨタ生産方式を代表する4つの仕組み
・トヨタにおけるPDCA
・トヨタ生産方式を導入するポイント
[/aside]
※この記事を書いた人
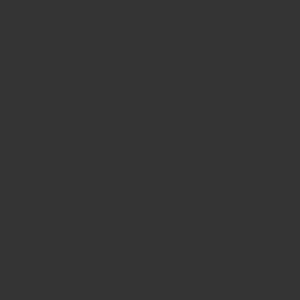
トヨタの生産方式とは
まずはじめに、トヨタの生産方式とは何かを見ていきましょう。
トヨタの生産方式には、「自働化」と「ジャスト・イン・タイム」という2つの考え方があります。
自働化
「自動化」ではなく「自”働”化」です。「ニンベン」、人の手が加えられた自動化という意味です。 機械化と区別して「人間の知恵を付与することで、不良品を生産しない」仕組みのことをいいます。
例えば、トヨタでは人間が作業を行う工場の生産ラインで、「問題があれば機械を止めて、問題の原因を調べて改善する」ことになっています。 不良品を検査で発見するのではなく、そもそも不良品をつくらないようにするというのがトヨタ生産方式の発想です。
生産ラインは機械化が進んでおり、各工程は自動化されています。機械であっても異常によりミス(不良品)が発生します。そこで、トヨタ生産方式では生産ラインに異常が発生した時、生産を止めて原因を究明します。 機械が異常を自動的に検知した場合、その内容を迅速に担当者へ通知します。ラインを止めるのはこのタイミングです。この後は担当者が原因究明にあたります。
このような改善活動を行うことで不良品の発生を抑えることが可能です。
つまり自働化とは、生産の大きなムダである不良品を作らない仕組みを構築することを指します。
ジャスト・イン・タイム
ジャスト・イン・タイム とは、「必要なものを、必要な時に、必要なだけ」手に入れることで、「ムラ・ムリ・ムダ」がなくなり、生産効率が上がるという考え方です。
”ムラ”とは、業務量にバラツキがあることです。”ムリ”とは、心身や設備に過度の負荷がかかること。”ムダ”とは、何ら付加価値を生まないコトやモノのことです。順番に正解はないのですが、トヨタでは「ムラ・ムリ・ムダ」といわれています。「ム”ラ”・ム”リ”・ム”ダ”」の「ラムダ」と覚えると良いでしょう。
「必要なものを必要な分だけ」生産することで、生産に関するムダを無くすだけでなく、品質の低下やばらつきを無くすことができ、計画どおりに無駄なく商品を生産できます。これを実現するための手法が「かんばん」方式です。
「かんばん」方式とは、情報伝達と生産指示の役割を果たすために生まれた手法です。部品の納入時間や数量が記載された作業指示書を使うことで、計画どおりに無駄なく商品を生産できます。
「かんばん」方式が大いに注目されたことで、「トヨタの生産方式」ではなく「かんばん方式」と呼ばれることもあります。
ジャスト・イン・タイム の考え方は、市場に「必要なものを、必要な時に、必要なだけ」届け、作業の中で余分なものを持たない、余分なものをつくらないことを基本にした生産・運搬の仕組みです。
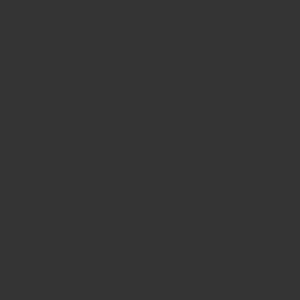
トヨタ生産方式を代表する4つの仕組み
トヨタの生産方式の考え方として、自働化とジャスト・イン・タイムを見てきましたが、この2つを実現するための4つの仕組みがあります。
[box class=”pink_box” title=”トヨタ生産方式を代表する4つの仕組み”]仕組みその①:改善仕組みその②:見える化
仕組みその③:「なぜ」を5回繰り返す
仕組みその④:7つムダ取り
[/box]
仕組みその① 改善
日々仕事をしているなかで、問題やムダに気づいたり、やりにくさを感じることがあるはずです。これらを常に「もっと良い方法はないか、ムダを省けないか」と考え続けることによって「良いやり方」を見つけることが「改善」の基本です。この時、お金よりも知恵を使って解決するのがトヨタの生産方式の改善の基本となります。
仕組みその② 見える化
問題を解決するためには、「みんなに見えるようにすることが大切だ」というのがトヨタの生産方式の考え方です。
問題が起こったとき(不良品が出たとき)、機械を止めるのもそのためです。機械を止めれば、問題が起きたことがみんなにわかる(見えます)が、問題が起こった時(不良品が出たとき)脇に置いたまま機械を動かしていれば誰にも問題が起きたことがわかりません(見えません)。これでは問題を解決するための知恵が出ることはありませんよね。
見える化というのは、問題をみんなに見えるようにし、みんなで知恵を出し、みんなで解決するための仕組みです。
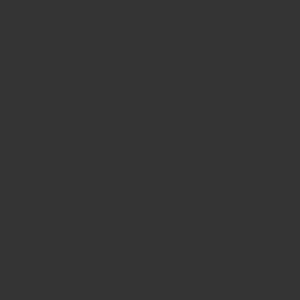
仕組みその③ 「なぜ」を5回繰り返す
トヨタでは、問題が起きた時、責任の追及よりも原因の追究を重視します。
「なぜ」をとことん繰り返して「真因」を見つけ、つぶす改善をしなければならないというのがトヨタ生産方式の考え方です。
問題が起きたとき、「なぜこの問題が起きたのか?」に対する「なぜ」の追求が甘いと、表面的な原因を「真因」と思い込んで対策をとることになります。それでは本当の原因をつぶしていないため、同じような問題が再び起きてしまいます。
”5回”とありますが、真因がわかるまでとことん”なぜ”を繰り返すのがトヨタの問題解決の基本です。
仕組みその④ 7つムダ取り
トヨタの生産方式はムダを徹底的に排除することが基本です。ここで言う”ムダ”は付加価値を生まない作業です。
ムダを無くすには、7つあるといわれるのムダを省きます。
トヨタでは、ムダを7つ挙げています。(加工のムダ、在庫のムダ、つくりすぎのムダ、手持ちのムダ、動作のムダ、運搬のムダ、手直しのムダ)。
これらのムダを無くすためには、各ムダを単体で考えるのではなく、全体のバランスや生産性を考えて無くしていきます。主に生産現場のムダを無くしますが、間接部門にも同じようなムダが発生していることも多いため、注意が必要です。
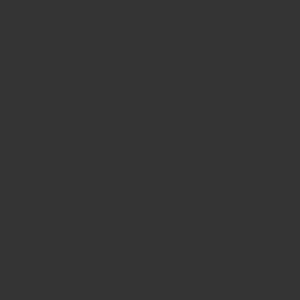
トヨタにおけるPDCAの流れ
それでは、この記事の本題であるトヨタにおけるPDCAの流れを見ていきましょう。
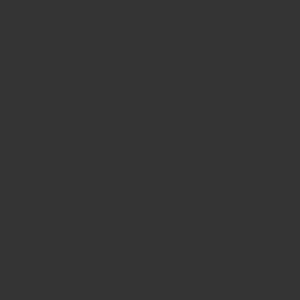
トヨタにおけるPDCA PLAN
「PLAN」(計画)としてはもちろん「トヨタ生産方式」を採用します。
「ムラ・ムリ・ムダ」を排除して生産効率を高め、最短時間で車を製造するシステムを構築しました。
トヨタにおけるPDCA DO
DO(行動)では、自働化と、ジャスト・イン・タイムの導入です。
トヨタにおけるPDCA CHECK
「CHECK」(検証)では、不良品が発生したり、問題が起こった時点で機械を停止。”なぜ”を繰り返し真因を検証します。
トヨタにおけるPDCA ACTION
「ACTION」(改善)では、CHECK(検証)で得られた真因を改善したり、作業を進めていくうえで良いことや、できることはすぐに取り入れるという企業文化を作りました。
こうしてトヨタは画期的な組織の構築や、市場へのサービス強化を進めることに成功し、日本を代表する世界的な企業としての地位を築きました。
トヨタ生産方式を導入するポイント
トヨタ生産方式は、効率よく生産のムダを排除できるため、現代の企業にとってもメリットの大きい手法です。そのため、多くの企業が取り入れていますが、失敗しやすい手法でもあります。
実際に、ジャスト・イン・タイムを導入した場合、運用を誤ってしまうと、在庫切れになってしまい、販売機会の損失になります。また、一度に大量生産することで、コストメリットが出る製品には、最小限の生産しか行わないと、原価が高くなることもあります。
トヨタの生産方式は、万能な方式ではないのです。
トヨタの生産方式をすべて取り入れるのではなく、自社に適した部分を採用し体制を見直すことが大切です。
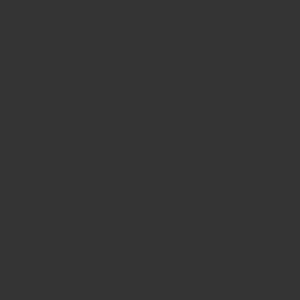
まとめ
トヨタの生産方式は、ムダを排除し、在庫を最小限にすることができます。
しかし一方で、現在の生産体制との相性が悪ければ失敗してしまうことも多い手法です。現場や改善箇所を把握し、自社に適した部分のみを採用することも効果的でしょう。
この記事を通して、皆さんの業務の改善につながればうれしいです。